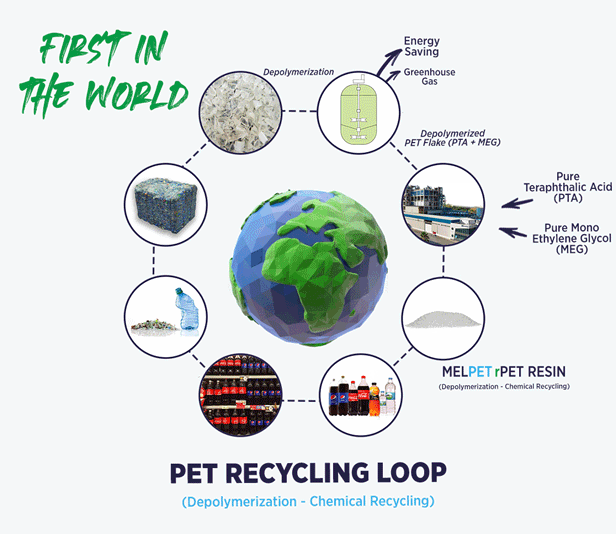
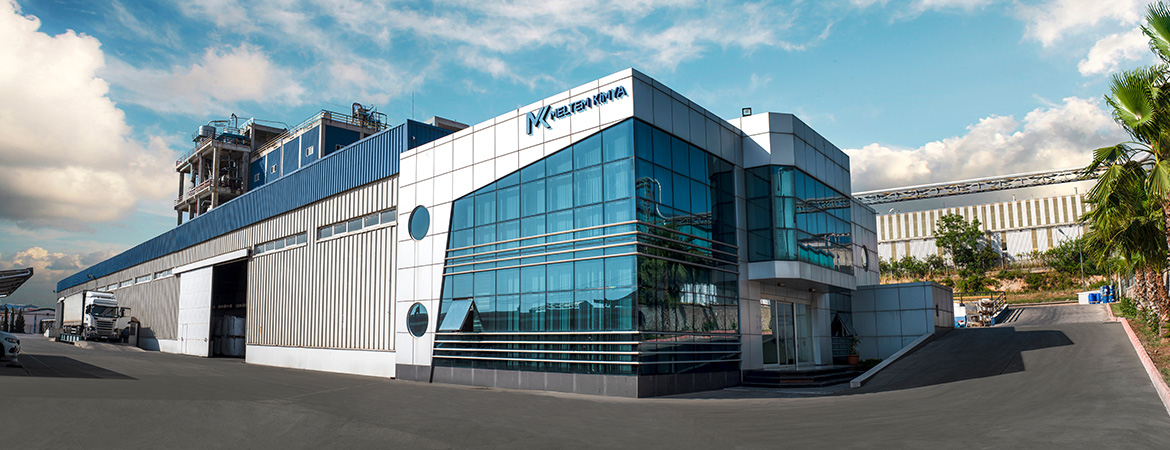
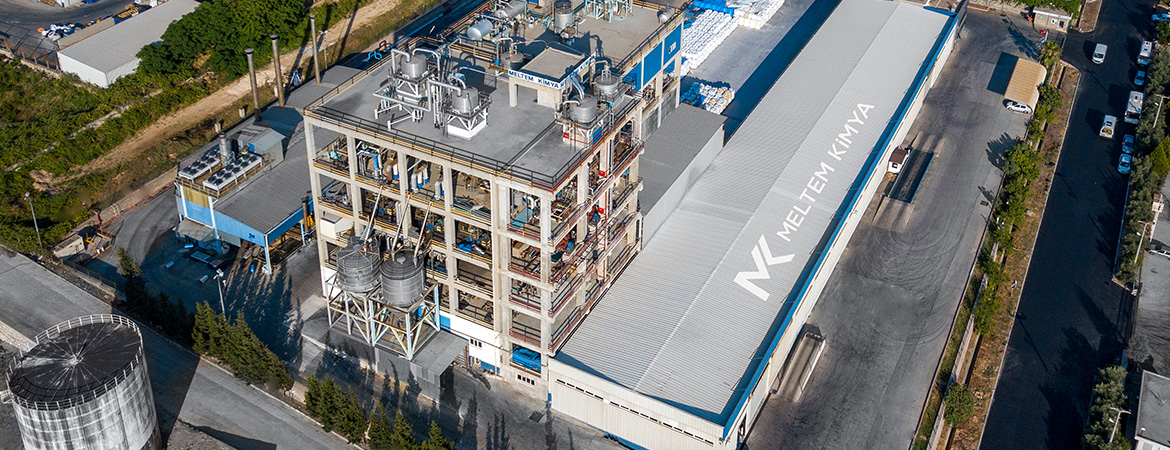


✓ Chemical recycling of used plastic bottle flakes by depolymerization method in glycolysis system.
✓ rPET content up to 50%.
✓ Valid for all commodity grades (in the range of 0.64 IV – 0.86 IV).
✓ Can be used for CSD (Carbonated Soft Drink), water, hot-fill, BOPET film and textile applications.
✓ Produced from hot-washed high quality PET flakes used as food packaging.
✓ Can be used in rapid thermal-processing applications with Fast Reheat additive as an option.
✓ Generates less carbon footprint compared to original PET.

rPET Production Method of Meltem Kimya
Chemical Recycling (depolymerization) is the conversion of PET polymer into its monomers, which are the smallest part of the polymer chain, by the glycolysis method. High quality PET flakes obtained from PET bottles which were used for food and beverage are removed from contaminants; sorted out by colors; and disinfected by hot washing by the approved and licensed suppliers who deal with collection, separation, fraction and washing arrive at Meltem Kimya. Although the PET flakes are of high quality, they are not taken into the depolymerization process directly. First of all, these PET flakes are made suitable for depolymerization method in our high-tech classification and conditioning facility in order to minimize PVC, other plastics and impurities. Then the classified and conditioned PET flakes are conveyed to our PET resin production facility. There; polymerization of the oligomers-monomers (small molecules of polymers) that are conversed by depolymerization (chemical recycling) method is completed by inclusion of original raw-materials in certain proportions; then the rPET resin, which is the raw-material of PET food packaging, is manufactured. The rPET resin released to the market is turned into PET bottles and used as packaging suitable for food. Thus, a full-cyclic and potentially infinite recycling solution is created
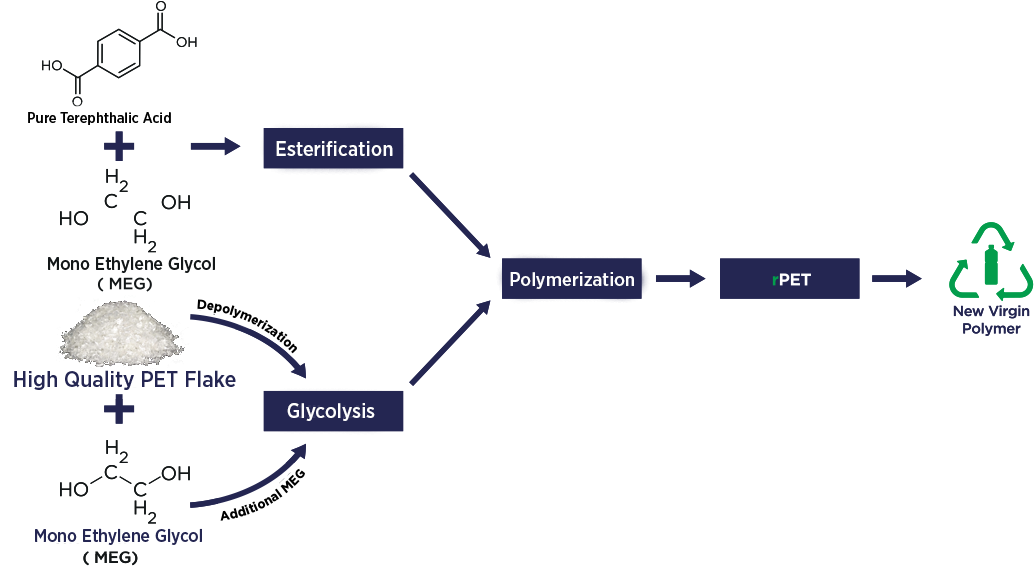
Meltem Kimya has been producing rPET resin by depolymerization (chemical recycling) of high quality and hot washed PET flakes which obtained from Food Contacted Post Consumer Bottles in glycolysis system.
Unlike the original resin, products made of rPET resin are environmentally friendly as they require less natural resources. Products made of rPET resin are recyclable and they contribute to the sustainability cycle. There are several ways to recover (recycle) PETs. The most common methods are mechanical (physical) recycling and chemical recycling.
Mechanical recycling of PET bottles is a procedure of reproduction of the washed packaging flakes in granule form by melting at certain temperature and pressure. The granules obtained are processed as they are or by being mixed with original pet resin. Since PVC impurities can be found in packages produced from the raw materials manufactured by mechanical recycling and it may threaten the human health, it is forbidden to use this method in Turkey, and is not allowed by the Turkish Food Codex. Packages to be produced by mechanical recycling can be recycled only seven times in nature.
Chemical recycling is one of the most important methods in recycling PET bottles. The purpose of chemical recycling is to completely remove the contamination and impurities of the PET flakes by depolymerization method in the glycolysis system. Chemical recycling is an important step towards achieving a circular economy. We complete the zero-waste cycle by recycling used beverage bottles and producing raw materials (rPET resin) that can be reused in food-compatible PET packaging with the appropriate method, thus move towards a healthier and sustainable future. Packages produced by chemical recycling method can be recycled infinitely.
Chemical depolymerisation method; is the reaction of recycled PET with enough ethylene glycol at over 200°C temperature and under pressure. In the glycolysis unit, the reaction is repeated several times until polymerization is reversed to bring out bis(2-hydroxyethyl) phthalate (BHET) and short-chain polymers. The BHET is then completely removed from impurities in the molten state under temperature and pressure.
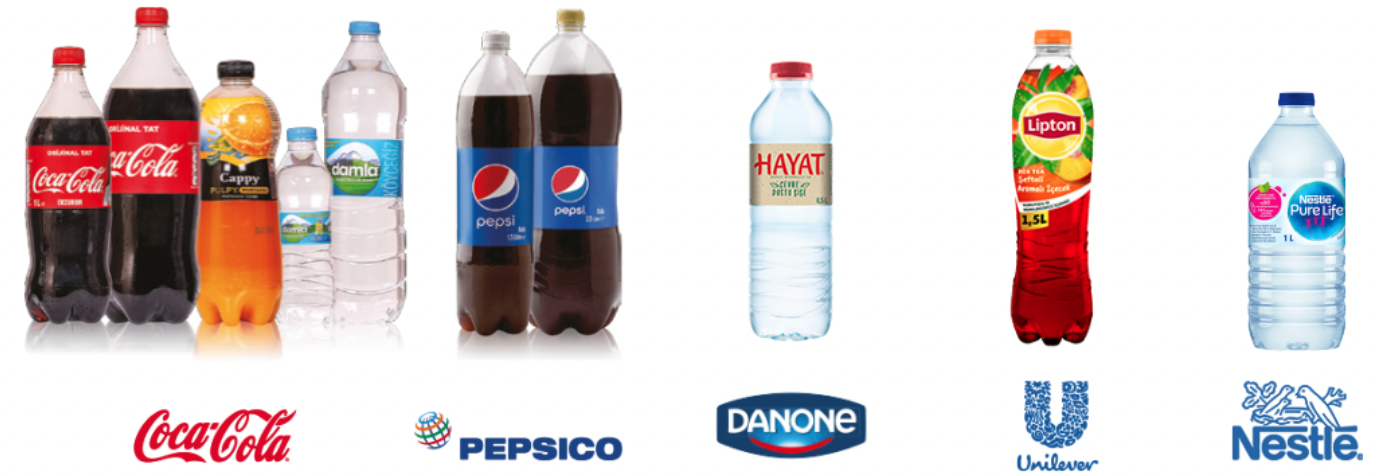